NDT SERVICES
Non-destructive testing (NDT) is a testing and analysis technique used by industry to evaluate the properties of a material, component, structure or system by detecting characteristic differences or welding defects and discontinuities without damaging the original part. can be detected. NDT is also known as non-destructive examination (NDE), non-destructive inspection (NDI) and non-destructive evaluation (NDE).
Thickness measurement
A popular and non-destructive thickness measurement technique commonly used to measure the thickness of a material from one side. This technique is called ultrasonic thickness gauging.
There is Following NDT measurement techniques are used
- Ultrasonic Thickness Measurement (UTM)
- Electromagnetic Acoustic Transducer (EMAT)
We have successfully carried out thickness measurement in major power plants.
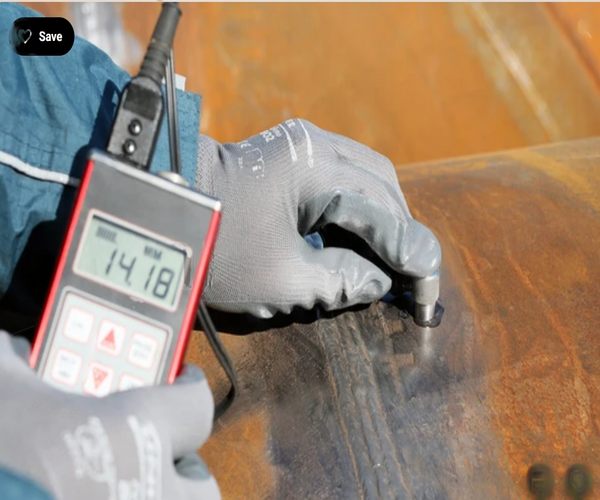
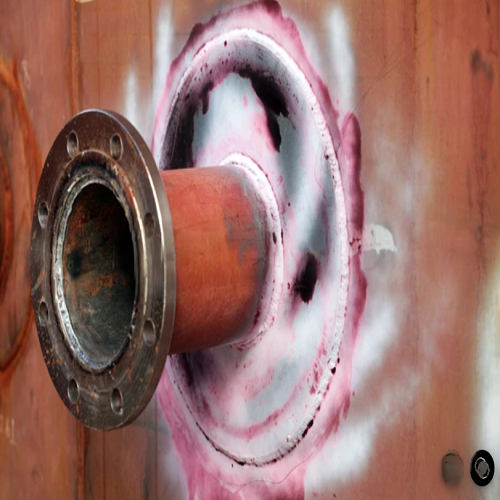
Dye penetrant testing
Liquid penetrant testing, also known as dye penetrant inspection (DPI) or liquid penetrant inspection (LPI), is one of the most common and economical solutions to non-destructive testing.
The principle of the liquid penetrant test is that the liquid penetrant is drawn into the surface breaking crack by capillary action and then the excess surface penetrant is removed, Then A developer is applied to the surface to draw out the element that has entered the crack and indicate the surface. Cracks as narrow as 150 nanometers can be detected. The indications generated is much wider than the actual fault and therefore more easily visible.
Magnetic particle testing
Magnetic Particle Inspection Technique (also known as MPI) is one of the most efficient techniques in NDT for ferro magnetic samples. Ferromagnetic substances are those that can retain their magnetism even after the applied magnetic field is removed. This is in contrast to paramagnetic materials in which the magnetism disappears when the applied magnetic field is removed.
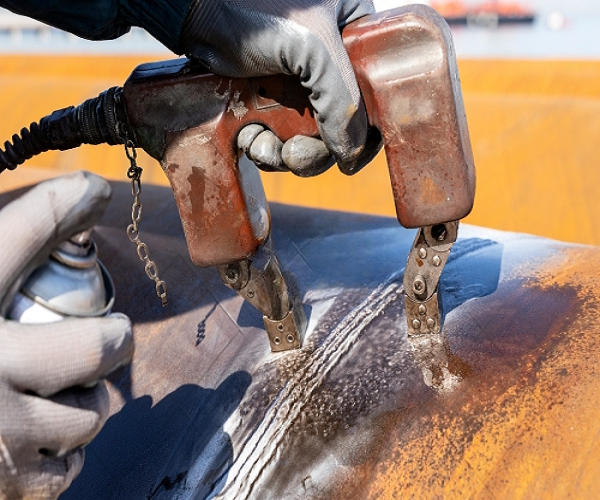
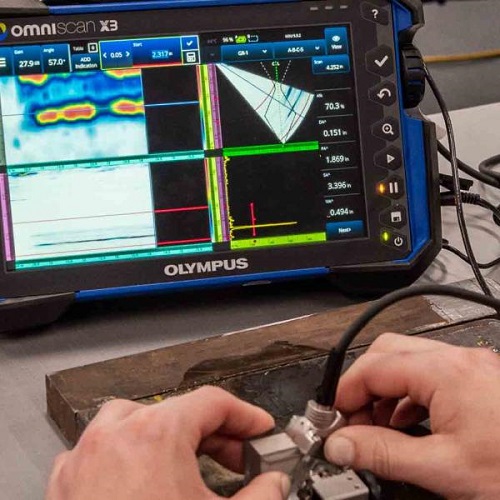
Phased Array Ultrasonic Testing (PAUT)
Phased Array Ultrasonic Testing (PAUT) is an advanced non-destructive testing technique that utilizes an ultrasonic probe capable of pulsed elements individually at varying time intervals.
Ultrasonic phased array testing uses multiple ultrasonic elements and electronic time delays to generate and receive ultrasound, forming a beam by constructive and destructive interference. Thus, Phase Array offers significant technical advantages over conventional single-probe UTs: the phased array beam can be electronically steered, scanned, swept and focused.
PAUT provides a higher probability to detection any defects, it is faster, more reliable, and it provides a permanent record of inspection through 2D or 3D images and recorded data.
Ultrasonic testing
Ultrasonic non-destructive testing, also known as ultrasonic UT, is a method of characterizing the thickness or internal structure of a test piece through the use of high frequency sound waves. The frequencies, or pitches, used for ultrasonic testing are many times higher than the range of human hearing, typically in the range of 500 kHz to 20 MHz..
High frequency sound waves are very directional, and will travel through a medium i.e. steel piece until they encounter a boundary with another medium such as air, at which point they are reflected back to their source. By analyzing these reflections, it is possible to measure the thickness of the test piece, or to find evidence of cracks or other hidden internal imperfections.
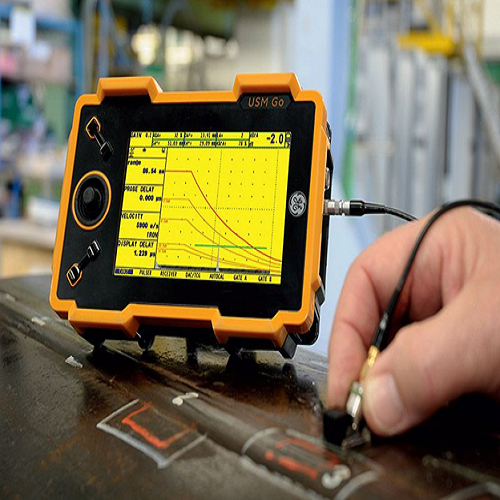
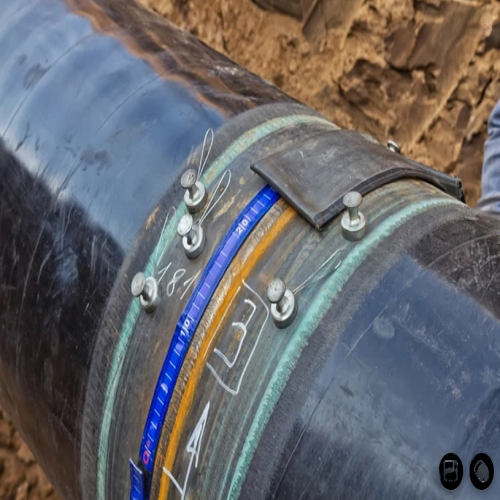
Radiography test
Radiography testing is one of the non-destructive testing techniques (NDT) employed for the investigation of engineering structures without compromising the structural integrity.
In radiography testing, the test-part is placed between a radiation source and a film. The difference of material density and thickness of the test-part will attenuate the penetrating radiation through interaction processes involving scattering and/or absorption.
There are two different radioactive sources available for industrial use; X-rays and gamma-rays. These radiation sources use higher energy levels, i.e., shorter wavelength, versions of electromagnetic waves. Due to the radioactivity involved in radiography testing, it is extremely important to ensure that local regulations are strictly followed during the operation.